The transportation system in the world has undergone tremendous technological advancement in recent times. These technologies have been able to solve many of the problems that people face when accessing transportation needs in their daily life. New transportation technologies are emerging to meet these challenges, including connected and autonomous vehicles, alternative fuels, keyless fleet management, and traffic analytics, as well as local zoning and planning policies that support transit-oriented development. Innovations in transportation technology are essentially born out of three necessities: efficiency, ease, and safety. Scientists and transportation industry professionals work side-by-side to ensure that these new technologies get more people (or things) to their destination faster, safer, and with the fewest amount of resources possible.
It’s worth seeing the latest and unique technologies that the world use today and how effective they are in the sense of transportation, economy, and even tourism. Let’s go with the simplest to most complex systems implemented by different countries.
Content
Busses
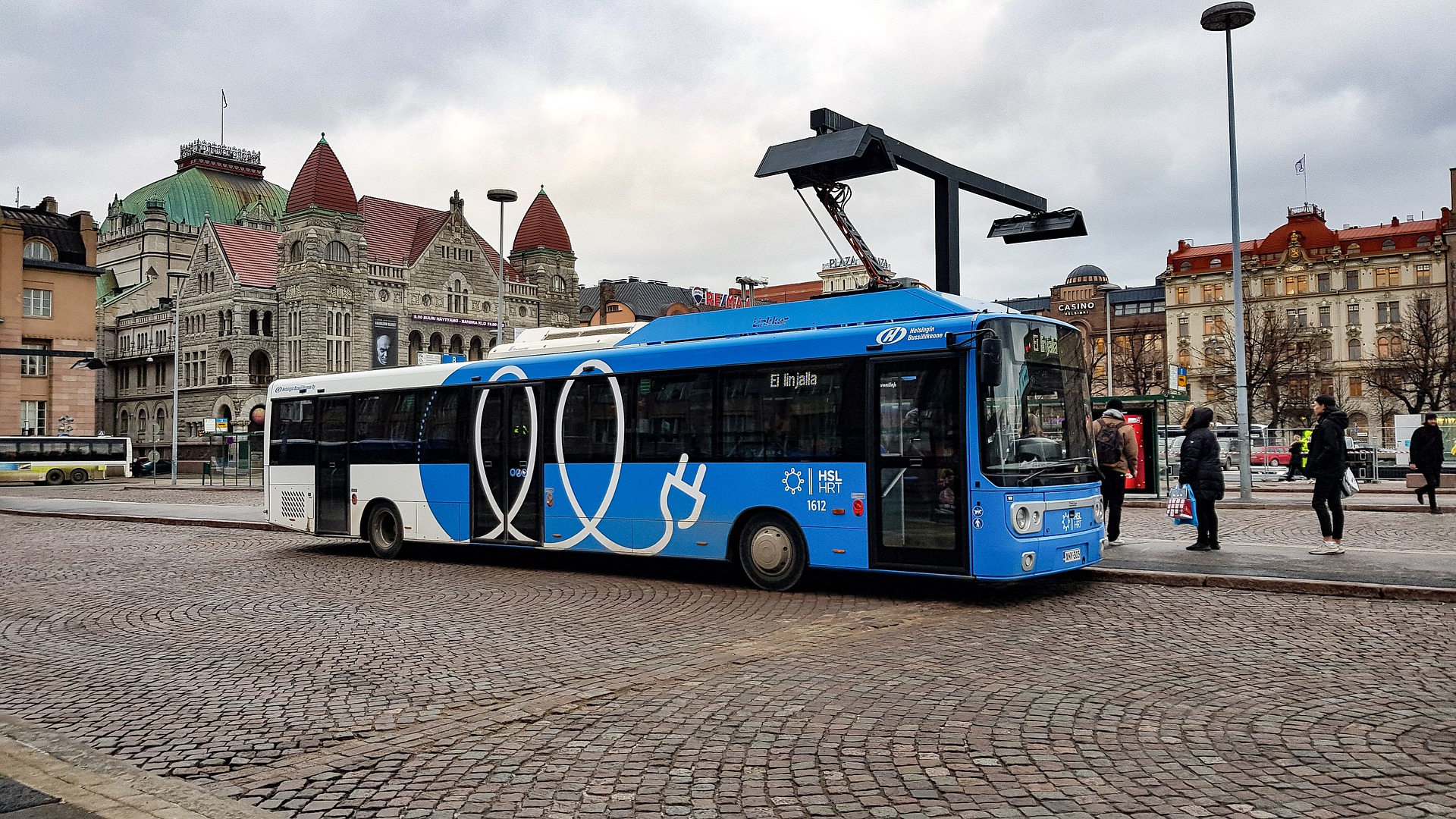
Electric
Electric bus adoption in public transport urban fleet is growing all over the world. It started in China, and it has taken a few years for other regions to start the transition. But now Europe is booming. The year 2019 will be remembered as the year when the electric bus sales volumes definitive ramp up.
Electric buses are also attractive because they support efforts to reduce local air pollution (“Doctors call for a ban on diesel engines in London,” 2016). Urban air quality is attracting increasing attention globally, and several international cities are moving to ban diesel vehicles from inner-city roads over the next decade (Harvey, 2016). Even new, efficient diesel engines
emit dangerous substances such as nitrogen oxides (NOx) and particulate matter (PM10). These pollutants are of particular concern in dense urban areas with high numbers of pedestrians and cyclists, which are typical of the conditions in which buses operate. Alternative bus powertrains that reduce or remove the need for a diesel engine, while retaining the advantages of buses, are of growing interest, especially in dense urban environments.
Hybrid electric, fuel cell electric, and full battery-electric buses are currently being used in a number of public transport networks around the world. Different types of electric bus technology vary in terms of whether electrical energy is generated or stored onboard, specifically:
Hybrid electric buses (HEBs) generate electricity onboard during operation using a diesel engine.
Fuel cell electric buses (FCEBs) use hydrogen fuel cells to generate electricity on-board during operation.
Battery electric buses (BEBs) store electricity onboard and are charged either overnight or intermittently throughout the route (Mahmoud, Garnett, Ferguson, & Kanaroglou, 2016).
Figure 1 outlines the main components involved in each electric bus technology option. Specific advantages and disadvantages to each type of powertrain will be discussed in their respective sections below, while a set of common advantages and disadvantages across all types of electric buses are outlined here4.
ADVANTAGES
- Emissions, less greenhouse gas (GHG), and local pollutant emissions.
- Reduced vibration, increasing passenger comfort and reducing damage to surrounding infrastructure.
- Noise, electric motors produce less noise than internal combustion engines (ICEs) and do not keep running when a bus is stationary.
- Fuel efficiency, all types of electric buses usually demonstrate increased energy efficiency.
DISADVANTAGES
- Cost, electric bus options are currently more expensive to purchase than their diesel alternatives.
- Infrastructure, electric bus options require different types of additional infrastructure.
Hydrogen
The Clean Hydrogen in European Cities project (CHIC) was a flagship zero emission bus project that deployed a fleet of fuel cell electric buses and hydrogen refueling stations in cities across Europe and at one site in Canada. The project started in 2010 and ended in December 2016. The project successfully demonstrated that fuel cell buses can offer a functional solution for cities to decarbonize their public transport fleets, improve their air quality and lower their noise levels. The buses can operate with the same flexibility as a diesel bus without compromising the productivity of public transport.
Fuel cell buses are a type of electric bus. They share many components with battery-electric buses, such as electric motors and associated power electronics. However, rather than storing energy in large batteries, fuel cell buses use hydrogen as fuel. The fuel cells consume hydrogen and oxygen to generate electricity through an electrochemical process, producing only water and heat as by-products, which then powers the electric motors. Hydrogen offers a much higher energy density than electrical storage systems (batteries and supercapacitors), meaning fuel cell buses can comfortably operate for an entire day of service without refueling. Modern fuel cell electric buses generally incorporate a small battery or supercapacitor as a part of the drivetrain, which improves the performance of the fuel cell and the overall energy efficiency of the bus, for example by boosting acceleration and allowing recuperation of braking energy. Apart from these differences, the bus structure and the other non-electric components are the same as in conventional buses.
Trams
Trackless Tram
Both bus and light rail technologies have been developing in recent years. Recent light rail vehicles also now feature onboard batteries or super-capacitors enabling wire-free operation (with re-charging at stops), as well as regenerative braking (to save energy), 100% low floor access (improving customer convenience and accessibility), and improved steering technologies for improved ride quality. P.R. China’s CRRC (now the world’s largest rolling stock manufacturer) has combined all of these advances into its new “Trackless Tram”.
This is an articulated, high capacity “Tram” running on rubber tires but with an in-built guidance system offering autonomous optically-guided running and operation. It is battery-powered (with recharging at stops or at the end of the trip), avoiding the necessity for overhead wires along the route. It is fully low-floor but uses improved suspension systems providing high ride quality. It has low axle loads, minimizing the need for expensive guideway infrastructure. It can also operate on regular streets because of its tight turning radius and high hill-climbing ability.
A Trackless Tram based system blends the best features of bus and train systems, both in the carriage technology and the system configuration to deliver a substantially more affordable option. For instance, the Trackless Tram carriage effectively starts with a standard light rail carriage that is narrow and has multiple entry doors with a turning radius and grade-climbing ability comparable to a bus and then provides four new attributes:
- It harnesses electric drive systems and onboard battery technology to avoid the need for overhead cabling or a fossil fuel engine, with recharge at either stations or end of run areas for longer periods;
- It substitutes the steel wheels of a train with rubber tyres. This avoids the need for rails and reduces the associated disruption of local economies due to extended period of construction works on roads and underground services for traditional light rail systems;
- It provides stabilization technologies through train-type bogeys with low set axles and hydraulic systems designed to prevent sway and bounce; and
- It adopts autonomous technology through optical guidance systems to provide precise and smoother ride quality and precision entry to stations and ease of boarding and lighting at platforms by passengers.
Considering the system configuration, the Trackless Tram System uses a dedicated corridor to provide rapid transit services that are supported by fixed stations and a Control Centre, much like light rail or traffic management centers. This provides the benefits in terms of city-shaping provided by traditional light-rail systems. However, the technology provides the flexibility to enable Trackless Trams to be diverted around blockages or quickly recalled should the need arise, unlike an LRT.
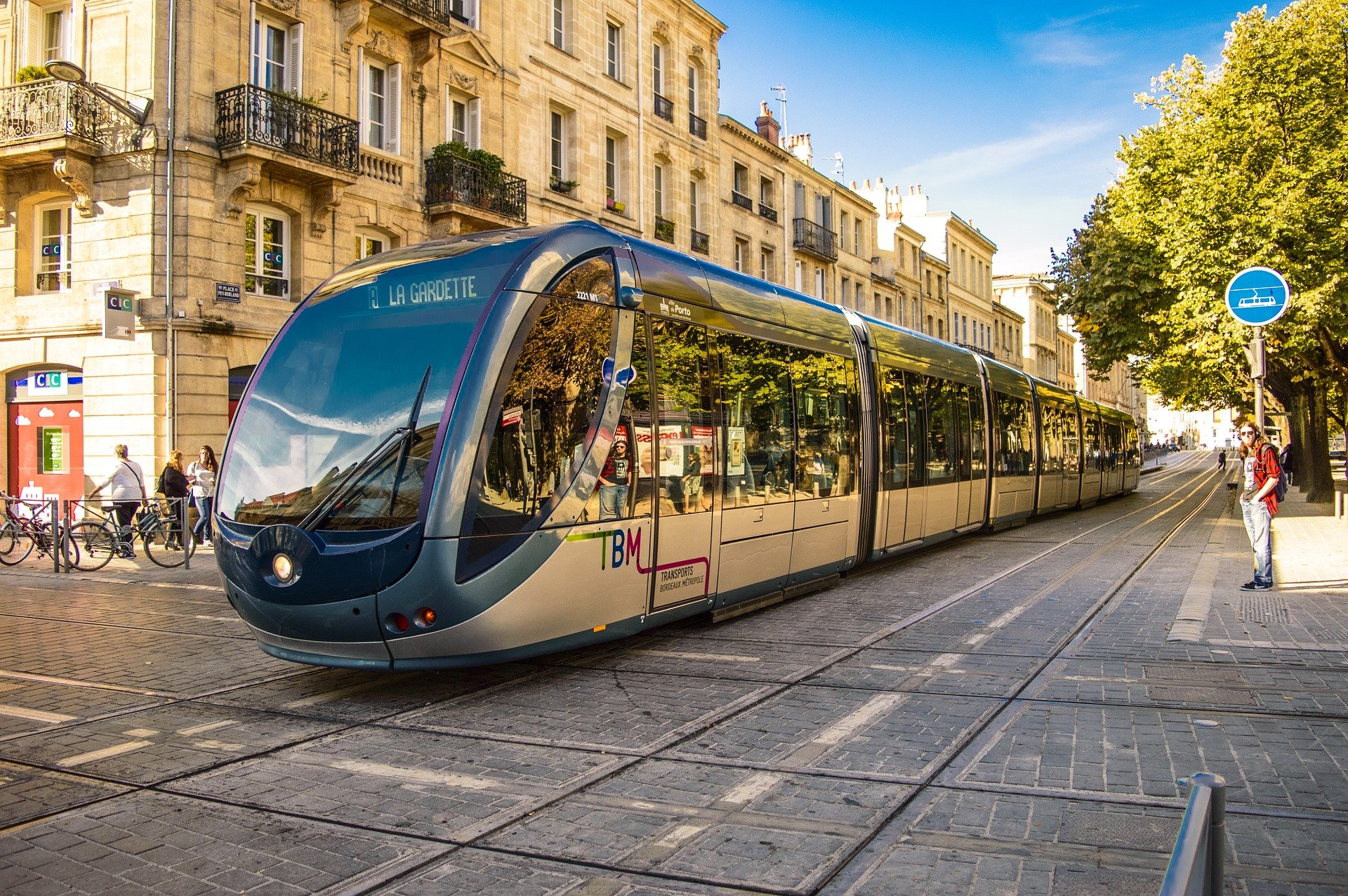
PRIMOVE Light Rail Trams
PRIMOVE Light Rail Trams are designed based on the PRIMOVE Solution from Bombardier. PRIMOVE is a path-breaking technology that makes modern urban transport cleaner and more convenient than ever before.
The trams use energy-efficient technology to preserve the environment. The urban transport technology also cuts CO2 and noise emissions. The technology is compatible with other transport systems, such as busses and cars too.
The wireless charging technology of PRIMOVE eliminates the constraints of complex infrastructures such as wires and plugs. The PRIMOVE system provides an appealing and affordable alternative to unpractical battery swapping techniques and reduces the ownership and maintenance costs.
PRIMOVE technology is developed based on the principle of inductive power transfer. The electric current that is fed to the primary winding in the wayside components of the system creates a magnetic field. This magnetic field induces the electric current in the coil present in the onboard components of the vehicle.
The phenomenon doesn’t essentially require contact between the two systems. The generated electric current is used for the propagation of the vehicle. The primary coil is extended in a loop along the track so that the secondary coil in the vehicle can receive power across the whole length of the loop.
The PRIMOVE tram system is connected with the Bombardier MITRAC energy saver system which permits power optimization for peak performance. The systems store energy during braking in double-layer capacitors and feed it back to the power system.
The PRIMOVE system can provide a power output varying from 100kW to 500kW depending on factors including length, the number of cars, geographic conditions, and the range of application. It is a typical light rail vehicle with length varying from 30m to 42m, gradient up to six percent and speed up to 50kmph running on 270kW power.
Trains
Automated Metro Systems
Self-driving cars have captured the imagination of the tech world and all leading automotive brands are racing against imminent legislature to get fully autonomous cars on the roads. Following straightforward railway tracks rather than navigating the comparably complex traffic jams, zebra crossings and cyclists of modern roadways seems easier, however we are likely to travel in a self-driving car before a self-driving train. Although, inner-city metro systems have been using Automatic Train Operation technology to transport citizens since 1967. This has both reduced jobs and the potential for frustrating closures due to drivers unpredicted absence.
Self-driving Passenger Trains
For high-speed, long-distance rail travel self-driving technology is further away than you might expect, this is because it’s harder to manage the stoppage distance of trains over long distances than of any other vehicle type. Trains need to identify stations or obstacles well in advance before making a calculated stop. To make matters worse, the friction between a train’s metal wheels and metal tracks is far lower than that between a car’s tyre and the road. So, coming to a quick stop needs human oversight, and achieving full automation would require far more advanced image processing technology than is currently available. That technology would then need to pass more rigorous reliability tests than self-driving cars, before being legally allowed to control public transport, because although both are terrible, a car crash has nowhere near the destructive potential of a train wreck.
Train Surveillance
Companies such as Eurotech are providing next-generation CCTV systems specifically for use on the rails, to meet global demand for increased railway security. An innovation introduced in 2009 in Japan utilizes blue coloured LED panels placed at the end of station platforms to prevent suicide, this proved so useful in the suicide capital of the world that it has been adopted elsewhere, including the UK. A study in the Journal of Affective Disorders found that the technology resulted in, on average, an 84% decrease in the number of suicides.
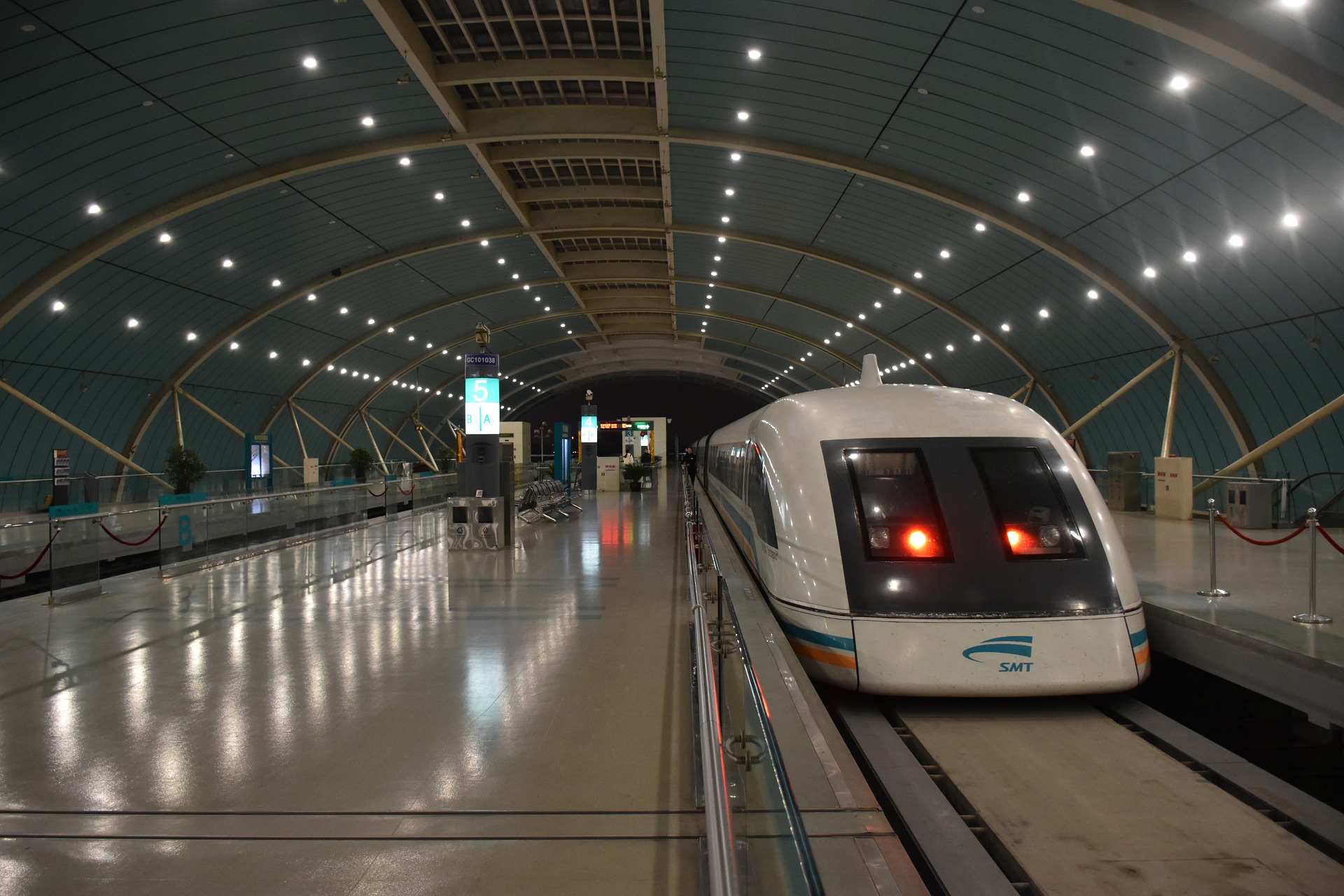
Train sets and locomotives
State-of-the-art high-speed (HS) trains don’t follow the traditional rules of the rails. Older trains still use one or two locomotives that contain all the traction motors and locomotives are positioned in the front as a pair, or the front and rear to better distribute the tractive forces.
Modern HS trains, however, put traction motors in almost every car for better force distribution and a more-comfortable ride. Distributing power over more axles also lets trains accelerate and decelerate faster. That’s because the powered wheels rely on friction between the wheels and rail to transmit power. Sending all the power to only two or three axles, especially when starting out from a dead stop, increases the likelihood that the power would overcome the friction and spin the wheels. There are also conditions, even with distributed power, when there’s not enough friction to get a large train rolling or up an incline. Ice or wet leaves, for example, can severely limit the frictional force and cause wheels to slip. To overcome this, HS trains carry dry sand, just like their slower-speed cousins. It gets dropped in front of powered wheels to increase frictional forces.
Power
Most HS trains get electricity from overhead wires or catenaries using a pantograph. Today’s batteries could never be sized to supply the power needed and still fit on the train. Diesel engines turning generators is not considered environmentally friendly and the weight and storage of diesel fuel, along with fire safety, would pose other problems. Another option, using a shoe to take electricity from a third rail, much like light rail, creates too much friction between the shoe and rail at high speeds.
Braking
Like most electric cars, HS trains feature regenerative braking, that is, using the traction motors as brakes, which generates electricity. And usually this electricity is fed back through the overhead lines so it can power an accelerating train on another track or get stored for a short time before being used by another train. There’s not enough room to store recouped electricity efficiently onboard the train and it rarely gets fed back into the national grid. When there is no place to store or use the electricity, it gets burned off in roof-mounted braking resistors (rheostatic braking) or the train switches to friction braking.
While regenerative braking is preferred because it minimizes wear and tear and saves energy, trains also carry electropneumatic friction brakes outfitted with steel discs and sintered pads designed for high loads.
Siemens’ Velaro train features linear eddy-current brakes. They consist of electrical coils positioned along the rails and held about 7 mm above them. The coils serve as magnets, but their north and south poles are continually switched. When the magnets move along the rail, their changing magnetic field creates another field in the metal rail, which creates electrical tension and eddy currents. The interaction between the coils’ magnetic fields and eddy currents they create in the wheels provides enough resistance to slow the train. Eddy-current brakes work fine at high speeds but are not viable at low speeds.
HS trains have two levels of emergency brakes. The first uses all forms of brakes onboard. In the second, called safety brakes, there is no electricity available, so only friction braking comes into play.
Aerodynamics and efficiency
Train designers are always striving to make their trains more aerodynamic. That’s because up to 60% of the tractive force can be lost due to drag and friction. Aerodynamics must also make the train stable because as speeds increase, cross-wind stability decreases.
Bombardier engineers use CAD and CFD to model as many as 60 design parameters. They concentrate on four basic areas: the lead car with its streamlined nose; spoilers atop and beneath the cars; stowing and deploying the pantograph; and fairings around the bogies, between cars, and covering the underside of the train. Fairings around the bogies also prevent track ballast and debris from damaging the wheels and axles. Through repeated efforts, Bombardier cut drag by 25%, which yielded a 15% drop in energy use and reduced the wind force on the lead car by enough to let them get rid of the 5 to 7 tons of dead weight the trains carried for ballast and stability.
Covering roof-mounted equipment with streamlined fairings also cuts drag, as well as limiting the “sonic booms” the exposed equipment can cause when trains enter a tunnel. The smoother roof cuts overall outside noise, too. For example, when passing another train at 186 mph, Siemens’ Velaro produces 91 dB(A) of noise. On the inside, passengers are exposed to only about 72 dB(A), thanks to sound-dampening coatings on the inside skin of the car and sound dampening on the air conditioner’s inlet ducts. There are also noise absorbers on the wheels, as well as air-spring bellows between the bogie and car body.
Maglev trains (Fastest Bullet Train)
SC Maglev or superconducting magnetic trains work on the principle of magnetic repulsion between the cars and the track. The word maglev is actually a combination of the words “magnetic” and “levitation.” The magnetic levitation, or floating of the train, is achieved through the use of an electrodynamic suspension system, or EDS.
The rails, or guideways, contain two sets of cross-connected metal coils wound into a “figure eight” pattern to form electromagnets. On the train, itself are superconducting electromagnets, called bogies. When stopped, the train rests on rubber wheels. To begin the motion, the train moves forward slowly on these wheels, allowing the magnets beneath the train to interact with those of the guideway. Once the train reaches 150 kilometers per hour (93 miles per hour), the magnetic force is strong enough to lift the train 100 millimeters (4 inches) off the ground, eliminating friction to allow for increasingly high speeds.
The same magnetic forces that lift the train also move it forward and keep it centered within the guideway. This is the same technology used by Tesla’s Hyperloop, which makes the ride smooth and the train exceptionally safe.
Cruises & Ferries
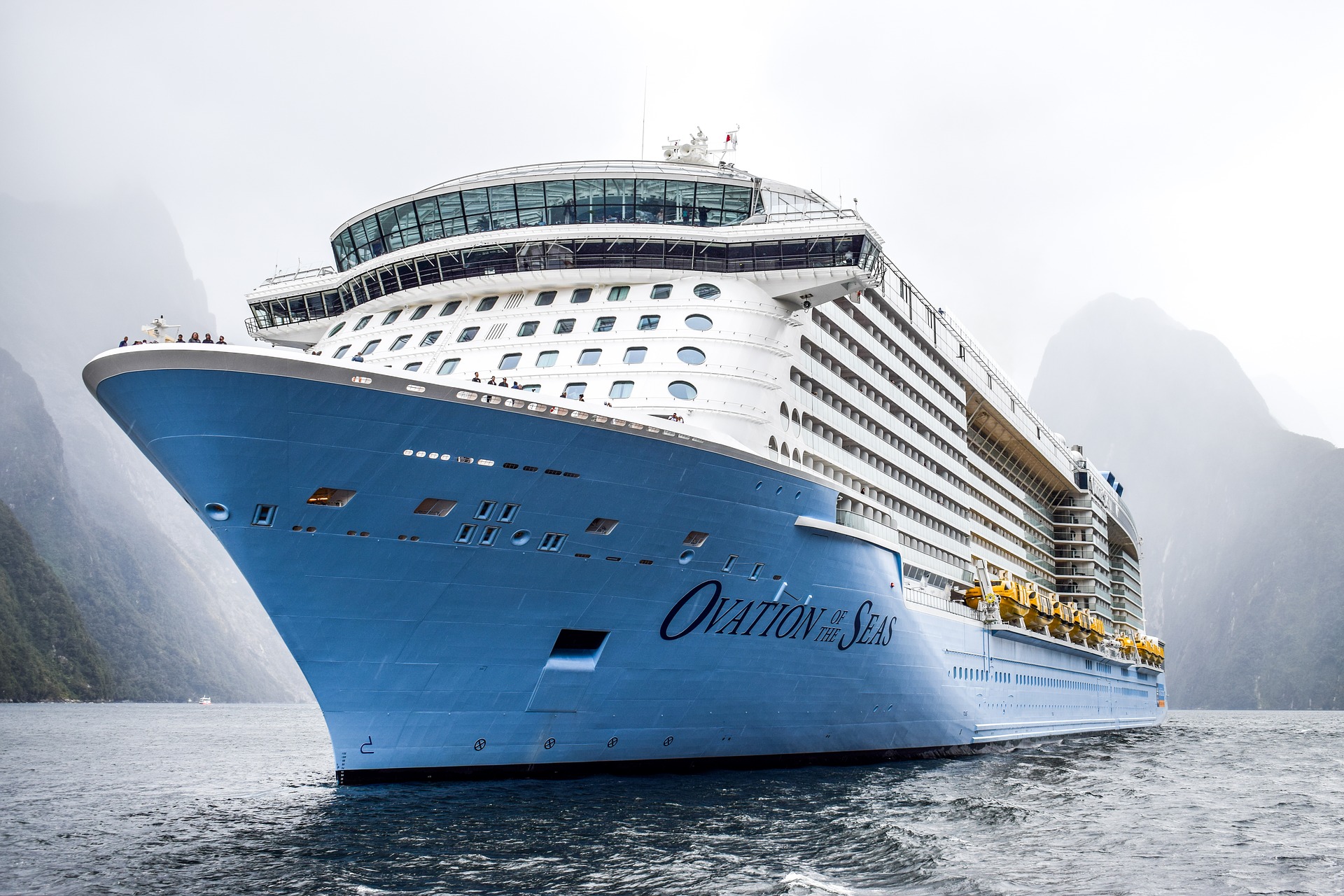
LTO batteries
The ferries are designed to meet the customer’s green goals, including increasing energy efficiency and reducing wake-wash. The E-LTO battery system was chosen for its optimal weight and safety, as well as its competitive pricing.
LTO is the safest maritime battery chemistry in the market – resilient to external heat and other abuse, preventing thermal runaways. It does not form dendrite like other lithium-ion chemistries, avoiding short circuits and increasing battery safety over time. E-LTO requires no active measures for water cooling or fire suppression. Propagation of thermal runaway between the Toshiba cells is almost impossible. E-LTO-batteries are completely air-cooled, which is an easy, safe, and robust system. There have been several fires involving water-cooled batteries that can be completely avoided with E-LTO batteries.
Rotor Sail technology
Rotor Sails, traditionally known as Flettner Rotors, were first installed on ships in the 1920s after being invented by Anton Flettner. At the time, the technology was not widely adopted due to the rising popularity and low cost of diesel fuel. Now, 100 years later, this wind technology has garnered new interest in its ability to help lower emissions. Wind power is a safe, sustainable way to propel modern merchant ships.
Rotor Sails have demonstrated increased vessel efficiency, reducing fuel consumption, bunker costs, and harmful emissions. Compared to other wind propulsion technologies, Rotor Sails offer a much greater thrust force to propel the shipper square metre of sail area. This means they can be made more cost-effectively and with less impact on vessel operation than traditional sails or wings.
The Flettner rotor sail concept works by harnessing the Magnus effect (see image below). According to this principle, wind pushing against a rotating, rounded object, such as a cylindrical rotor sail, creates motion perpendicular to the flow of the wind. When wind is flowing in the correct direction — sideways across the deck of the ship, perpendicular to the direction the ship is traveling in — and hits against the rotor sail, the rotation causes air flow to accelerate on one side of the sail and to decelerate on the other side. The different wind speeds on each side of the sail create higher and lower pressures on either side, which creates lift force, or thrust, perpendicular to the direction of the wind flow. This thrust propels the ship forward.
Hybrid ro-ro vessels
New ultra-green vessels will bring many benefits to our customers, including fast and efficient loading and unloading, and in addition, provide more flexible cargo space to our customers.
The vessels are designed to be flexible for all types of ro-ro cargo whilst tank top and main deck are designed to free of pillar areas to accommodate paper and sto-ro concept. Several decks and internal ramps speed up loading and unloading. At the same, the vessels will be an extremely flexible – hoistable deck makes it possible to load any type of rolling freight such as trucks, tractors, excavators up to 7.4 metres.
The vessels come with an integrated propeller-rudder system and modern hull lines that have been designed in accordance with the state-of-the-art hydrodynamics. They will be equipped with the most modern two-stroke main engines, which have a lower specific fuel consumption than four-stroke engines, and thus also, they produce less CO2 and other emissions.
In addition to lithium-ion batteries that enable zero-emission operations in the port, they will be equipped with emission abatement and an innovative air lubrication system to reduce hull resistance.
Additionally, the vessels will be equipped with approximately 600m2 of solar panels. Renewable energy is available onboard to users.
Airplanes
Winglets
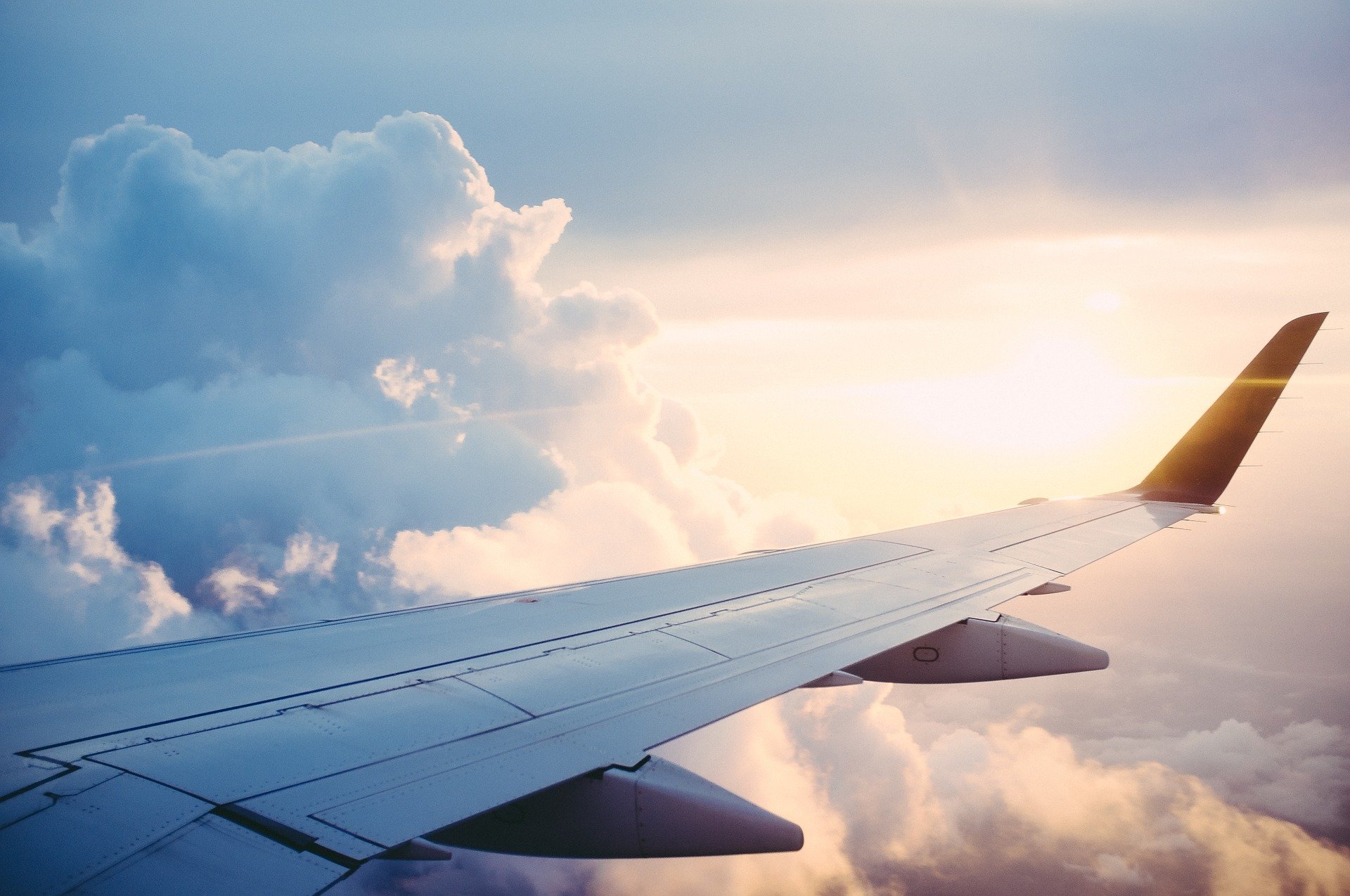
Winglets are devices mounted at the tip of the wings. Winglets are used to improve the aerodynamic efficiency of a wing by the flow around the wingtip to create additional thrust. They can improve airplane performance as much as 10% to 15%. An appropriately planned winglet at a slight point to the approaching wind and whirling stream around it causes “lift” on the winglet, which is coordinated internally along the wing and forward. Finally, by reducing drag, they can cut emissions by 6%.
3D Printing/Carbon fibers/Shape Memory Alloys (SMA)
The aviation industry has begun using 3D printing technology (additive manufacturing), carbon fiber materials, and shape memory alloys (SMA) because they all can reduce aircraft weight while increasing customization and overall construction efficiency. According to this report, the global aerospace 3D printing market is forecasted to grow at 55.85% CAGR during the period 2016-2020.
Shape memory alloys work through heat: at the required temperature, the alloy metal transforms into different shapes. SMA are being explored as vibration dampers for launch vehicles and commercial jet engines. Reducing the overall weight of the airplane is always a top priority to increase fuel efficiency.
Double-Bubble D8
In 2008, as part of NASA’s N+3 program, a team of engineers from Aurora Flight Science, MIT, and Pratt & Whitney started working on a design concept for commercial aircraft. They named it “double-bubble” D8, and if the new machine works as anticipated, it could substantially decrease commercial aircraft noise, emission, and fuel burns associated with commercial travel.
Unlike other passenger aircraft, D8 designs do not have an engine beneath the wings. Instead, the designers opted to place the engines on top of the plane body near the tail. This alteration dramatically reduces the drag and improves fuel efficiency. If the D8 is designed and implemented as planned all over the world, it will have huge potential to reduce aviation-related fuel consumption and will potentially reduce emissions up to 66% in 20 years
Wing Spars
The wings of a plane go through a lot of stress between take-off, cruising altitude, and landing. Any technological advancements that work towards alleviating that stress make flying safer for everyone on board. A wing spar is one of the most important components of a wing because it bears all of the stress. When a wing spar fails, the plane could crash.
Crews use ultrasound to monitor wing spars as well as fuselage skin to check for early signs of failure. The latest technology to avoid wing spar issues is resin-filled nano-structures. If engineers embed these structures into the wing spar material, they could patch cracks as soon as they form. This is key to protecting everyone on board.
Airport Surface Detection Equipment-X
The penultimate technology on our list is for control towers. The FAA’s Airport Surface Detection Equipment-X basically creates a continuously updated map of all airport traffic. It does this by integrating data from an inbound plane’s GPA unit and the transponder signals from ground vehicles and other planes in the air. That way pilots are aware of everything going on around them.
So, Since this is a large topic, we will bring you more pieces of information about Autonomous and Connected Vehicles, Booking and Ticketing, Smart Cities &, etc in our next review article. Meet you in the next article!